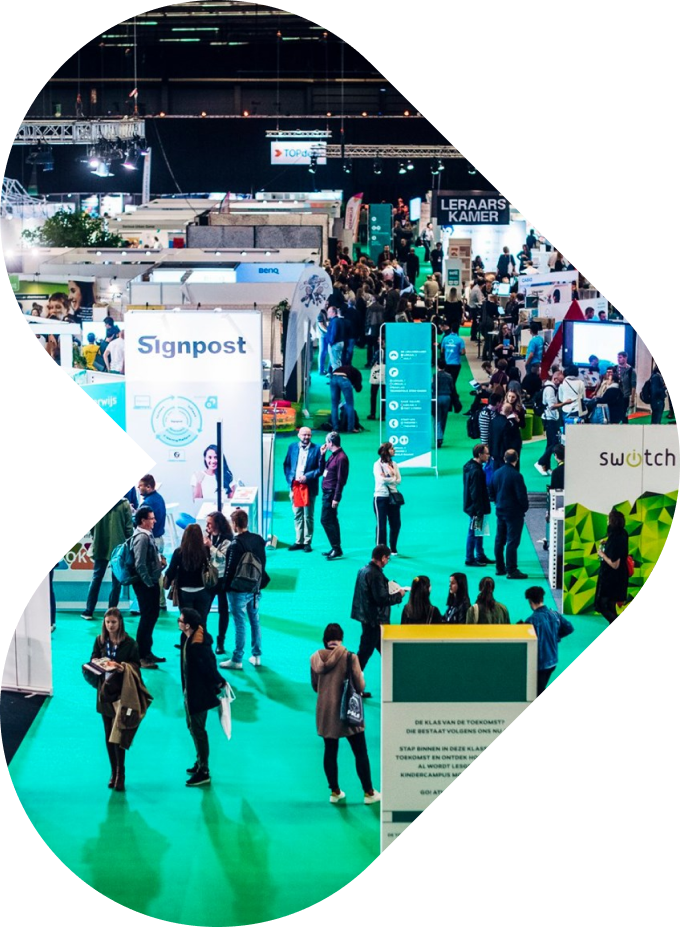
Join us on a journey into the future of events
What will your life and business look like in the future?
Our aim is to take you there. With a perfect mix of information, education, entertainment and networking opportunities.
The unrivaled power of face-to-face events
Only live events can engage all the senses. There’s no substitute for face-to-face meetings or connecting with peers in person. Nothing compares to discovering and testing new experiences by seeing, touching, hearing, smelling or tasting.
Today, in our post-covid, digital world, the human element is more essential than it has ever been. Live events are beyond compare. They’re real-life social media.
Community first
We do everything with a sense of fun and a passion for bringing business, professional and social communities together. Our events are not ‘small’ or ‘large’ they are simply the right multi-format fit for your community.
You are very welcome!
Our network of venues in Belgium, the Netherlands and Sweden are flexible, technologically advanced platforms for both Easyfairs and guest events. We host exhibitions, trade shows, conferences, concerts, sporting events – and more.
Whatever the occasion, we promise a great experience and a warm welcome.
Acting for the future
How we act for the planet
Caring for the planet is one of our core values. So, we’re doing more than reducing the environmental impact of our own events and venues. We’re also helping our communities in their transition to net zero by embedding sustainability and innovation in the content of our events.
How we act for society
We’re making a positive impact on society at at two fundamental levels. As a company, we’re helping our communities achieve net zero emissions and working with charitable organisations. As an employer, we’re committed to a diverse, inclusive workplace where every team member can thrive.
Life at Easyfairs
We are team players who have fun together while pursuing success. For us, the journey is just as important as the final goal.
Our awards and successes
#11 in top 20
Best Managed Companies
ESG Award
UFI Awards
Latest News
Easyfairs Nordic strengthens market position with acquisition of stand building business
Stockholm, 08/02/2024: Easyfairs Nordic announces the acquisition of the stand building business at Kistamässan venue from Workman Event. …
Read moreEasyfairs acquires Southern Manufacturing & Electronics
This acquisition represents a significant addition to Easyfairs’ extensive European engineering & manufacturing portfolio. London, 10/01/2024: Easyfairs, the …
Read moreEasyfairs announces 19% increase in revenues; EBITDA up 25%
“All lights are green” for leading events organiser Brussels, 7 November 2023: Easyfairs has announced its results for …
Read moreEasyfairs and QUiCKFairs join forces to form powerful partnership
This strategic acquisition adds two key events, namely Coiltech in Italy and Coiltech in Germany to the Easyfairs …
Read moreEasyfairs wins the 2023 UFI HR Award
Brussels, 3 August 2023 – We are proud to announce that Easyfairs has been selected as the winner of …
Read moreEasyfairs earns Best Managed Companies label for the fifth year running
Events company is now a Gold Requalifying Laureate Brussels, 12 May 2023 – Easyfairs has retained the Best …
Read more